Customer Partnership Support
Taking the guesswork out of your processing operations
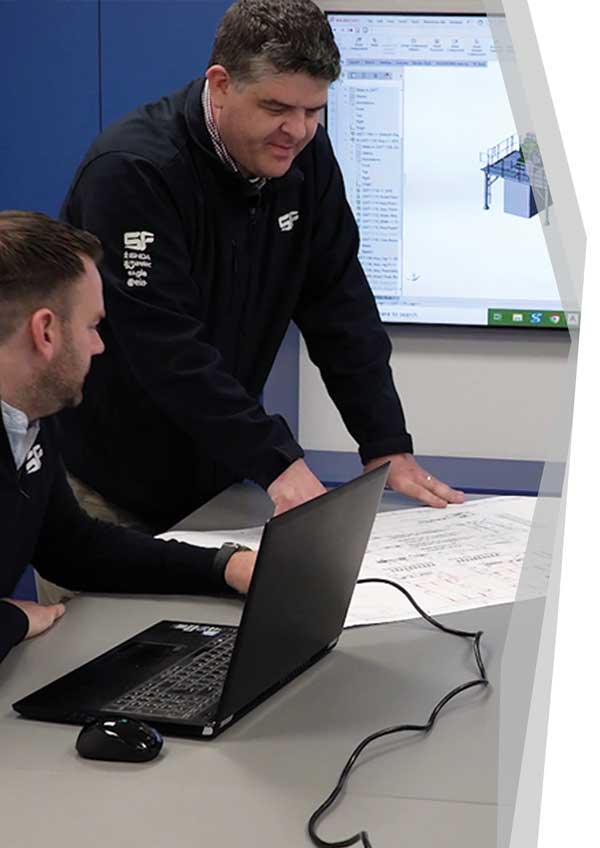
Partnership Support & Consultancy
Our wealth of knowledge across the food processing industry has proven to be the reason why customers return continually for our customer support and consultancy advice.
Whether the project is a feasibility study to increase product throughput and yield, an assessment to reduce product recalls or a greenfield site for a meat processing facility, we are called upon for our expertise in the latest processes and design proficiency.
If you are seeking capital approval for a new project or site, consulting with our experts can help you calculate:
- Expected throughput
- Improvements in yield
- Cost savings on labour and utilities
- Increased productivity
- Reduced giveaway
- Overall project costs
- Return on investment
Planning
The process planning stage is critical to ensure your project moves forward with minimal hold-ups and additional cost expenditures.
Our expert planning process, when carried out before design and manufacture, will help you to understand the full potential of your production lines.
It will also highlight any limitations, and production bottlenecks so these can be resolved early on, resulting in a complete future proof factory layout.
Assessing space, layout and accessibility, as well as putting in place project timelines, responsibilities and actions are key components undertaken by our planning team.
We focus continually on creating ecological and economically sustainable food processing solutions that are delivered on time and within budget.
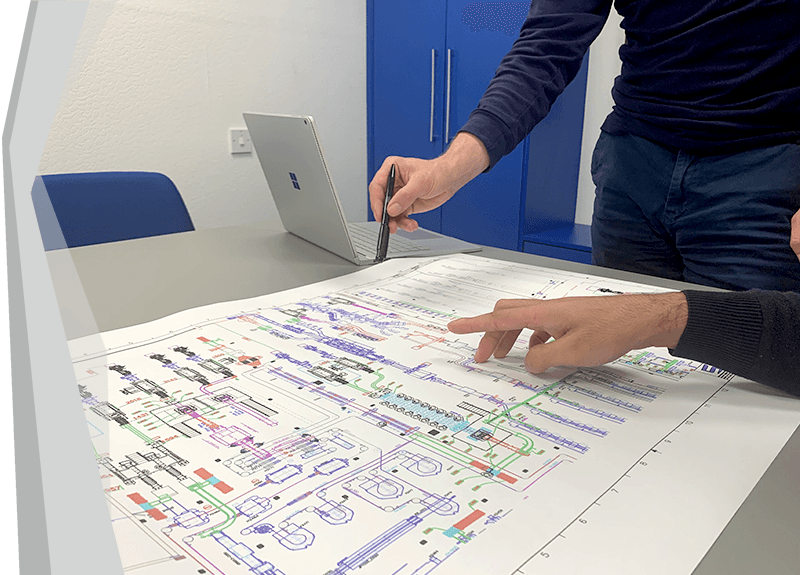
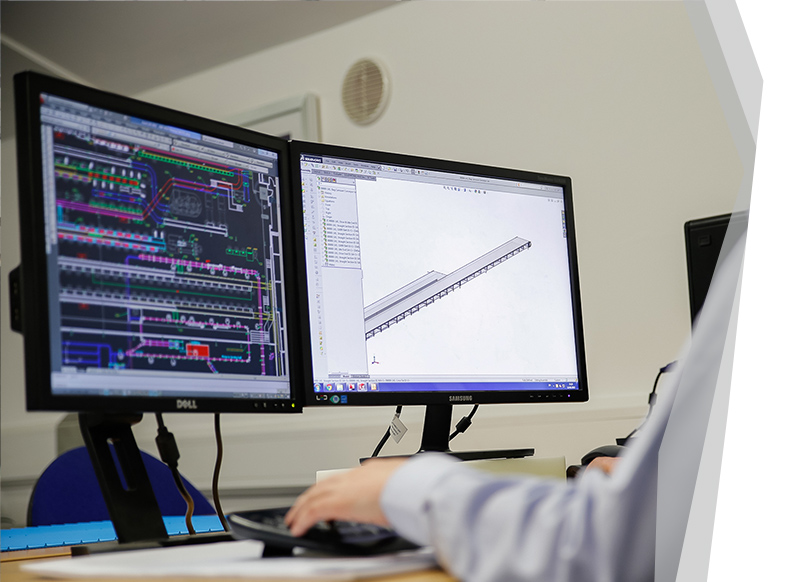
Design
Our designers are experts at optimising production, increasing efficiency and helping you maximise yield by providing the best equipment layout for your facility.
Through carefully composed staff training programmes, our design team understands the design approach from initial concept through to implementation.
This allows us to put in place solutions that reduce maintenance demands and consumable costs.
As standard, ergonomics, user safety, and hygiene are crucial factors to get right when designing a new food processing line. Our customer partnership support assesses continually every design from a user’s perspective.
This minimises unnecessary lifting, adhering to correct working heights and ensuring conveyor pinch points are safely guarded.
Project Management
Our Project Management teams focus continually on delivering high quality projects on time and to budget. By combining excellent leadership skills with technical know how and commitment, we drive projects through to successful completion.
Our Project Management teams are very familiar with the demanding conditions that arise across the food processing industry and have gained a vast knowledge of solving complex food industry challenges on a daily basis.
The responsibility of our project management team encompasses the full cycle from design, engineering, electronics, part and product selection, on-site implementation and ongoing maintenance. This ensures you get a consistent point of contact and expert customer partnership support on your project.
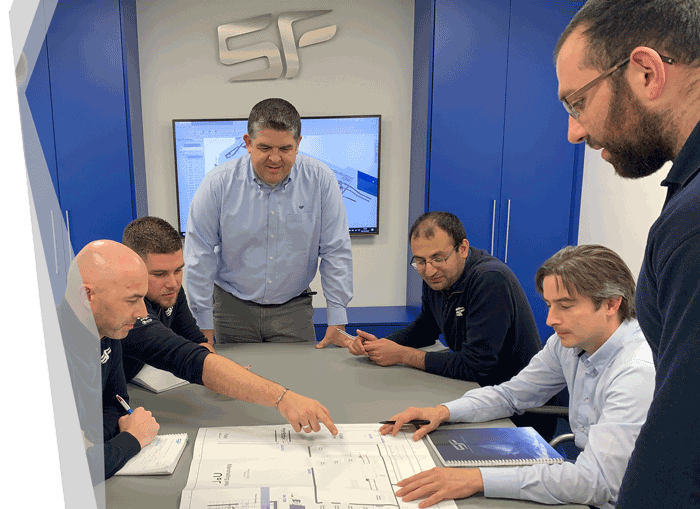

Manufacture
SF Engineering has state-of-the-art manufacturing facilities on the West coast of Ireland and in the East of England. We are positioned perfectly to serve the food industries’ operational needs around the world.
Our team of highly-skilled designers, engineers, fabricators, welders and assemblers work closely together to deliver the most advanced processing line solutions. Each system is fully assembled and tested before shipping allowing for adjustments, customer approval, product testing and training, as required.
We operate to the highest standards in relation to efficiency, health and safety. We use the highest quality materials that are fully compliant with industry regulations. This ensures the integrity and safety of equipment and finished solutions from point of sale to project hand over.
Installation & Commissioning
Our global installation team are highly skilled engineers who have a wealth of experience working in often challenging, food processing environments. Throughout the installation and commission process, the Commissioning Team work very closely with the Project Management Teams to ensure works are carried out efficiently and to exact requirements.
With their extensive knowledge of our processing line solutions, the Installation and Commissioning Teams are well placed to oversee the alignment, corrections and adjustments of all our systems.
Once the installation is complete, our Customer Partnership Support makes sure all the equipment meets the required industry standards and meets all requirements for the purpose it was installed. This includes visual inspection as well as testing and calibration of equipment.
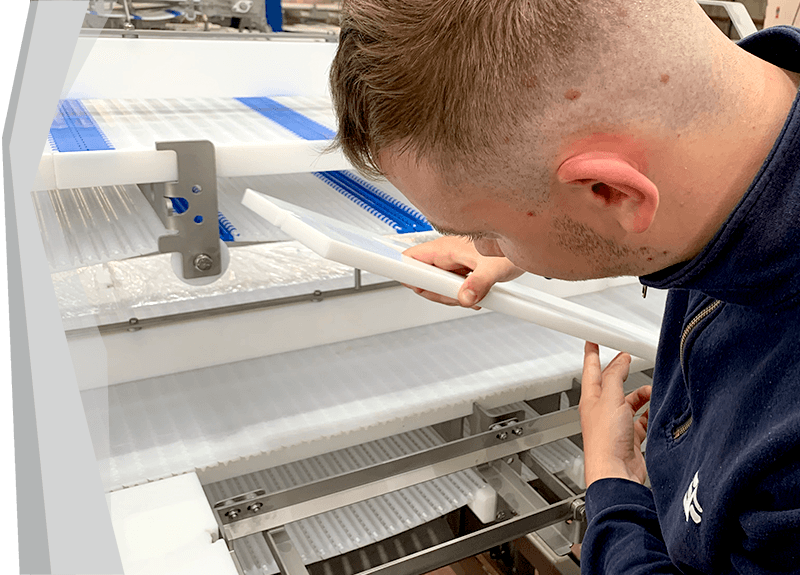