Video: Crate Decanting Solution
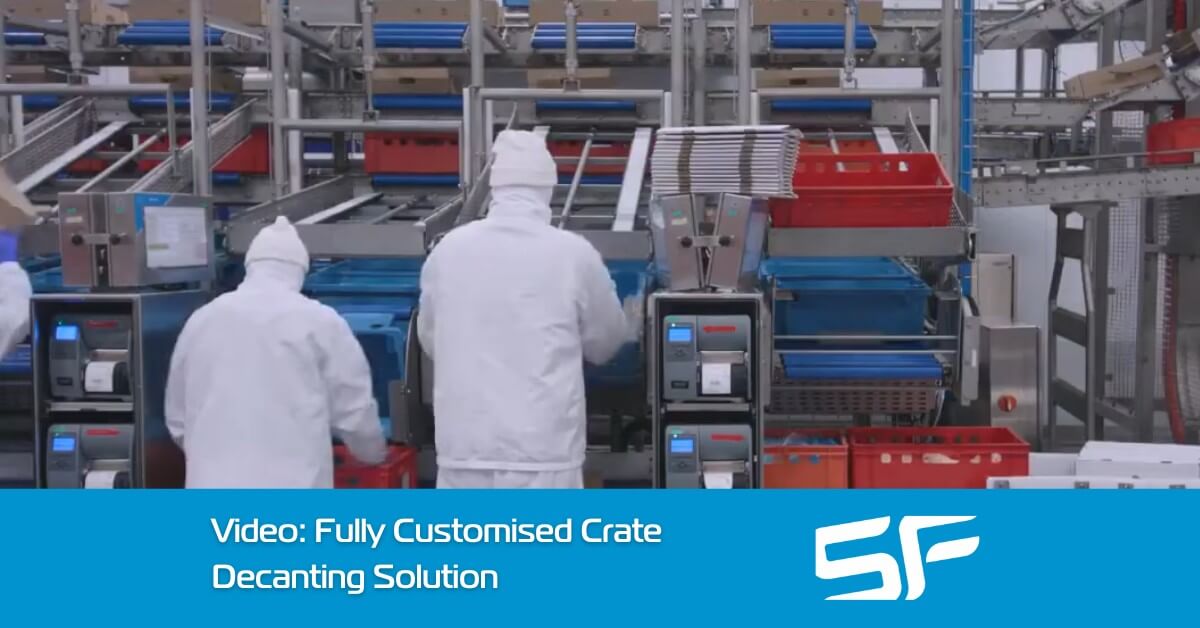
We recently completed the installation and commissioning of a crate decanting solution for a customer in the poultry processing industry. The crate decanting element was part of a wider project on a greenfield site. The factory is now operational, and processes large volumes of products packed in bulk for export and food service.
The objective of the crate decanting element of the project was to create a system to bring crates from all parts of the factory to a central location for final packaging. The customer wanted to achieve this with minimal operator involvement in the movement of crates. The system also had to accommodate different types of product, crate, and final packaging material.
Watch our video of the solution in action:
Automated Crate Decanting Process – Solution Explainer
Conveyors
Various types of poultry product are produced in the factory on different lines. After processing, the product is put in crates with an embedded RFID tag. The data in the RFID tag includes the product’s description, SKU, weight, and destination. Crates with decanting set as the destination are moved to the decanting area by conveyors.
Because of the way we designed the system, there is minimal requirement for operators to have to lift or carry a crate.
The conveyors transporting crates to the decanting area were also designed at a high level to enable walk access throughout the factory, minimising workflow disruption and optimising the available floorspace.
RFID Tag
The RFID tag is read by the PDM (product data management) system when the crate reaches the decanting area. The system automatically pushes the crate into the correct station based on the information in the RFID tag.
The RFID tag is automatically read again when it is in the decanting station and the data is used to identify the correct container for the product. One of three types of containers is then automatically selected by the infeed system and presented to the operator.
Up to this point in the process, there has been minimal operator involvement:
- Crates are transported to the decanting station by conveyors.
- The system automatically determines the correct decanting station.
- The system automatically determines the correct container.
- Both the crate and the container are automatically presented to the operator.
Decanting
With the correct crate and container in front of them, the operator presses a button to tip the crate forward. As the operator helps transfer the product from the crate to the packaging container, a label is automatically printed containing all relevant information – product, weight, customer details, etc. The operator applies the label to the container and pushes it onto a takeaway conveyor where it passes through a metal detector, checkweigher, and on to the palletising area of the factory.
The now empty RFID crate is placed on a separate conveyor for redistribution around the factory to be filled with more product. The RFID tag is read again as part of this process to limit the number of times a crate is reused before washing. Once the limit is reached based on the data in the RFID tag, the crate is automatically distributed for crate washing.
Benefits of the Decanting Solution
- Fully customised design according to the requirements of the customer.
- Reduction in the number of operators required compared to a manual decanting process.
- Capable of decanting and processing 40 crates a minute.
- Improved traceability compared to manual processes through the automated processing of data in the RFID tag.
- Optimised ergonomics for operators
- Human error is eliminated as crates, containers, and labels are presented to operators automatically based on the data in the RFID tags.
- Optimised hygiene through the automation of the decanting workflow and various processes. Hygiene and cleanability features were also designed into the solution.
- High-quality components are used throughout, from belts to bearings to motors.
Consultancy Expertise
This project not only demonstrates the advantages of an automated crate decanting solution for food processing facilities but also showcases our consultancy expertise. At SF Engineering, we have extensive experience solving complex food processing challenges and developing innovative solutions that work in real-world conditions and deliver tangible benefits from day one of operation. Get in touch to discuss your requirements and to find out how our team can help.