Quality Control Investment – 3 Key Factors to Consider
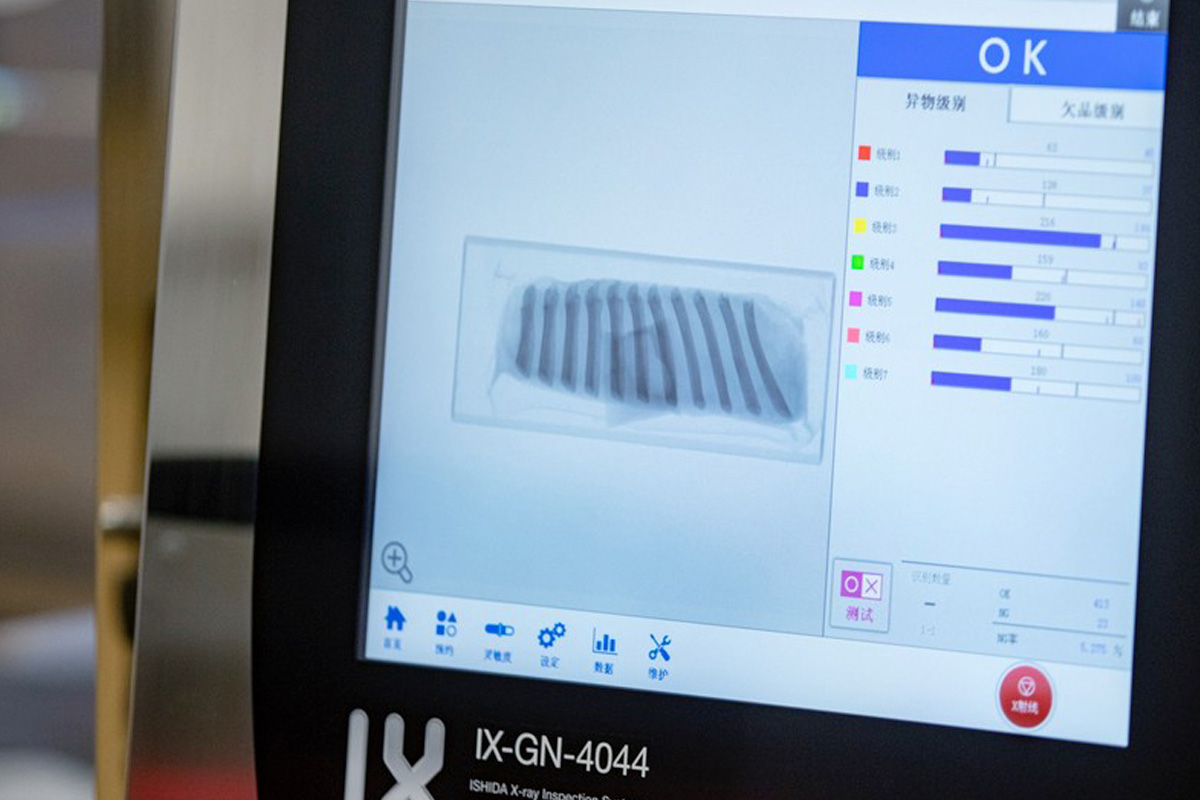
As a food manufacturer, you will understand the importance of maintaining a robust quality control practice to safeguard your consumers and brand reputation. We know the troubling impact that product recalls due to foreign body contamination, high levels of scrapped product or unnecessary giveaway have on your bottom line. That’s why it is important to select a quality control solution that effectively ensures a consistent quality product and maximum food safety within budget.
There are a number of inspection solutions in the marketplace that control different points along your production line such as X-Ray, Metal Detectors and Checkweighers. Each solution gives you peace of mind for your business and your consumers. But what key factors should be considered before making your next quality control investment?
Updating your quality control solutions
Whether you are looking at replacing existing quality control equipment on your current line or purchasing an entirely new quality control line, it is always best practice to plan for current and future processing requirements, key points to consider:
1. Performance of the inspection system
For X-ray systems you must assess that the machine sensitivity levels are above your current requirements, this will not only future-proof the line to cope with potential new product needs, but it will also reduce the amount of false rejects in your current production runs.
Product effect is an important factor when selecting a metal detector. If your products are conductive (usually due to water, salt, or iron content), they will affect the electromagnetic field of the metal detector, causing it to produce a false reject. A metal detector that uses multiple frequencies is more suitable for these applications. The most sophisticated metal detectors on the market use multi-spectrum technology.
Ensure your checkweigher is capable of exceptional sensitivity on a wide variety of product sizes and at different processing speeds. It’s important by providing accurate verification of a package’s weight or count and detecting missing components without compromising on efficiency.
2. Total cost of ownership
Total cost of ownership goes beyond the price of the machine, for this we must take into account the reliability of the system as well as factor in the cost of spare parts. When you imagine that the machine has the potential to be running for 10 years, for example, these are elements which can’t be ignored. To find out more about this topic read our blog, 8-factors to consider when calculating the total cost of ownership of your food processing machinery.
3. Compliance & Regulations
Look for a partner that can support you, who understands guidelines and procedures and can advise you on compliance and regulations.
Speak to the experts
SF offer expert support & advice to ensure your operation runs at optimum performance. Each of our processing and packing lines is carefully designed to offer the best possible throughput, improved product yield, more efficient product handling as well as improved accuracy, hygiene and safety.
Our partnerships with the world leaders in quality control inspection systems, namely Ishida and Ceia means we offer unparalleled inspection performance to suit the current and future needs of your business. From entry-level machines through to high-speed production environments, the main focus of each inspection solution we install, is to protect your customers and your brand.
Get in touch with our team: Ireland +353 71 9163334 Email: info@sfengineering.ie UK +44 1487 740131 Email: info@sfengineering.co.uk
Find out more visit about the Government incentive visit www.gov.uk